近年來,隨著全球經(jīng)濟(jì)技術(shù)的高速發(fā)展,產(chǎn)品的多功能化和輕便化的不斷推進(jìn),使得薄膜科學(xué)的應(yīng)用日益廣泛。而濺射靶材作為鍛膜產(chǎn)業(yè)的基本耗材, 其制備技術(shù)也得到了長足發(fā)展 。濺射薄膜由于其致密度高 ,附著性好,被廣泛應(yīng)用于裝飾、玻璃、電子器件、光學(xué)器件、 半導(dǎo)體、磁記錄、平面顯示屏 、太陽能電池、飛機(jī)葉片防護(hù)涂層等眾多領(lǐng)域。隨著上述領(lǐng)域的快速發(fā)展, 對靶材的需求量急劇增加, 同時(shí)對靶材的高質(zhì)質(zhì)量、大型化及利用率方面也提出了更高的要求。
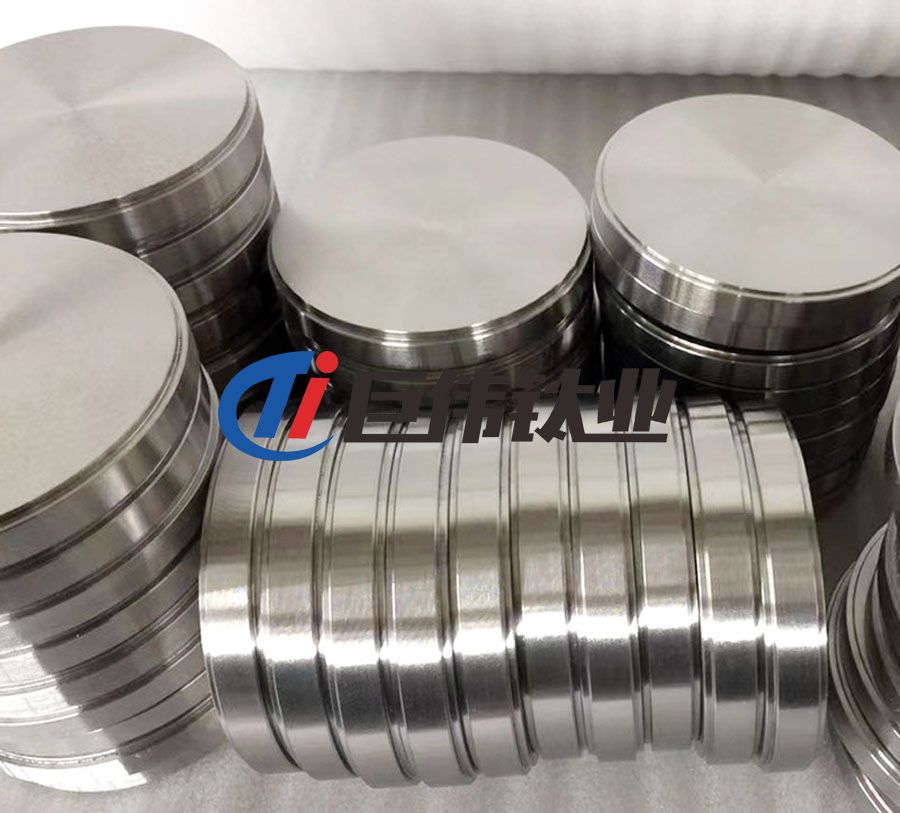
一、濺射靶材的特性要求
為了提高濺射效率和確保沉積薄膜的質(zhì)量,對濺射靶材特性有如下要求。
1、純度
高純度是對濺射靶材的一個(gè)基本特性要求。靶材的純度越高,濺射薄膜的 性能越好。一般濺射靶材的純度至少需要達(dá)到99.95%。濺射靶材作為濺射中的陰極源, 固體中的雜質(zhì)和氣孔中的氧氣和水氣是沉積薄膜的主要污染源。
2、致密度
濺射鍍膜的過程中,致密度較小的濺射靶受轟擊時(shí), 由于靶材內(nèi)部孔隙內(nèi)存在的氣體突然釋放 ,造成大尺寸的靶材顆?;蛭⒘ow濺 ,或成膜之后膜材受二次電子轟擊造成微粒飛濺。這些微粒的出現(xiàn)會(huì)降低薄膜品質(zhì)。為了減少靶材固體中的氣孔,提高薄膜性能 ,一般要求濺射靶材具有較高的致密度。對濺射靶材而言 ,其相對密度應(yīng)該在98%以上。
3、晶粒尺寸及尺寸分布
通常濺射靶材為多晶結(jié)構(gòu),晶粒大小可由微米到毫米量級。試驗(yàn)研究表明 ,細(xì)小尺寸晶粒靶的濺射速率要比粗晶粒快;而晶粒尺寸相差較小的靶,淀積薄膜的厚度分布也較均勻。
4、結(jié)晶取向
由于濺射時(shí)靶材原子容易沿原子六方最緊密排列方向擇優(yōu)濺射出來,因此,為達(dá)到最高濺射速率,常通過改變靶材結(jié)晶結(jié)構(gòu)的方法來增加濺射速率。
靶材的結(jié)晶方向?qū)R射膜層的厚度均勻性影響也較大。 因此,獲得一定結(jié)晶取向的靶材對薄膜的濺射過程至關(guān)重要。
5、靶材與底盤的綁定
一般濺射靶材濺射前必須與無氧銅、 不銹鋼或鋁等其他材料的底盤連接在一起,使濺射過程中靶材與底盤的導(dǎo)熱導(dǎo)電狀況良好。綁定后必須經(jīng)過超聲波檢驗(yàn),保證兩者的不結(jié)合區(qū)域小于2%, 這樣才能滿足大功率濺射要求而不致脫落。
二、濺射靶材的主要制備方法
濺射靶材按其材質(zhì)可分為純金屬靶、合金靶、陶瓷化合物靶(包括氧化物、 硅化物、 碳化物、 硫化物等)復(fù)合靶。按形狀可分為平面靶和管狀旋轉(zhuǎn)靶,平面靶又可分為矩形板和圓形靶。 目前, 雖然濺射靶材種類繁多但其基本的制備工藝主要包括粉末冶金法和熔煉鑄造認(rèn)兩大類 , 但隨著技術(shù)裝備的不斷進(jìn)步, 大功率的熱噴涂技術(shù)也逐步在靶材生產(chǎn)中得到了應(yīng)用。
1、粉末冶金方法
粉末冶金法包括粉末壓制燒結(jié)法、粉末熱等靜壓等。粉末冶金法是將粉體原料按比例混合均勻, 經(jīng)過壓制成形, 然后在高溫下燒結(jié), 經(jīng)壓力加工、熱處理后最終得到靶材。該類力法適合于難熔金屬如鎢、鉬靶材及陶瓷靶材的制備。粉末冶金法制備濺射靶材時(shí), 其關(guān)鍵于(1)選擇高純粉料作為原料; (2)選擇能實(shí)現(xiàn)快速致密化的成形燒結(jié)技術(shù),以保證靶材的低孔隙率,并控制晶粒度; (3)制備過程嚴(yán)格控制雜質(zhì)元素的引入。采用粉末冶金法制備的靶材具有成分均勻及晶粒均勻細(xì)小、成品率高的優(yōu)點(diǎn), 但制備過程采用粉末混合、壓制和燒結(jié)工藝,容易在制備過程中帶入雜質(zhì)元素, 燒結(jié)過程雜質(zhì)排除效果較差, 造成靶材純度相對較低, 并且燒結(jié)靶材的密度也較熔煉靶低。
2、熔煉鑄造法
熔煉鑄造法的基本工藝是將一定比例的合金原料熔煉后澆注到模具中形成鑄錠, 然后通過鍛造、擠壓或拉拔等成形工藝進(jìn)行加工, 最后經(jīng)過熱處理、機(jī)加工等工序制備得到濺射靶材。常用的熔煉力法有真空感應(yīng)熔煉,直空電弧熔煉和真空電子束熔煉等。與粉末冶金法相比,熔煉鑄造法得到的靶材純度高. 密度高, 但其工藝較為復(fù)雜對設(shè)備要求高, 成本也隨之升高。并且靶材晶粒粗大。若各組分之間熔點(diǎn)和密度相差較大, 則難以獲得成分均勻的合金靶材。
3、等離子噴涂方法
等離子噴涂是將金屬或非金屬材料粉末送入等離子射流中, 利用等離子火焰加熱融化噴涂粉末, 并在沖擊力的作用下將其沉積到基體上, 從而獲得具有各種功能的靶材。
三、等離子噴涂方法制造管狀旋轉(zhuǎn)靶材
在平面磁控濺射過程中, 由于正交電磁場對濺射離子的作用關(guān)系,濺射靶在濺射過程中將產(chǎn)生不均勻沖蝕現(xiàn)象,從而造成濺射靶材的利用率普遍不高, 約30%左右。近年來雖然通過設(shè)備改造可相應(yīng)提高靶材的利用率,但也只有50%左右。另外, 靶材原子被氬離子撞擊出來后,約有1/6的濺射原子會(huì)淀積到真空室內(nèi)壁或支架上,增加清潔真空設(shè)備的費(fèi)用及停機(jī)時(shí)間。因此,提高靶材利用率的關(guān)鍵在千實(shí)現(xiàn)濺射設(shè)備的更新?lián)Q代。另外一種提高濺射靶材利用率的方法是采用管狀旋轉(zhuǎn)靶材。相比平面靶材, 采用旋轉(zhuǎn)靶結(jié)構(gòu)的設(shè)計(jì)顯示出它的實(shí)質(zhì)性優(yōu)勢。從平面靶到旋轉(zhuǎn)靶在幾何結(jié)構(gòu)和設(shè)計(jì)上的變化增加了靶材的利用率, 利用率從平面靶的30%~50%可增加到旋轉(zhuǎn)靶的>80%。此外,如果以濺射功率乘以濺射時(shí)間來衡量靶材料的壽命,則旋轉(zhuǎn)靶的壽命要比平面靶長5倍。由于旋轉(zhuǎn)靶在濺射過程中不停地旋轉(zhuǎn), 所以在它的表面不會(huì)產(chǎn)生重沉積現(xiàn)象。
以傳統(tǒng)的粉末冶金和熔鑄方法在濺射靶材的制備方面雖然被廣泛采用, 但其共同的問題就是難以制備大尺寸(平面靶及管狀靶)的濺射靶材, 尤其對一些高熔點(diǎn)脆性材料更是如此。而靶材的大尺寸及高利用率的旋轉(zhuǎn)靶材巳經(jīng)成為了未來鎖膜領(lǐng)域的新趨勢。因此,開發(fā)新型的大尺寸旋轉(zhuǎn)濺射靶材制備方法已經(jīng)成為目前靶材制備領(lǐng)域亟待解決的問題。
1、等離子噴涂技術(shù)原理
等離子噴涂是利用等離子火焰加熱融化噴涂粉末使其形成涂層, 一般等離子噴涂使用Ar或N2氣, 再加入5%~10%的H2氣,氣體進(jìn)入電極區(qū)的弧狀區(qū)被加熱電離形成等離子體, 其中心溫度一般可達(dá)15000℃以上, 將金屬或非金屬材料粉末送入等離子射流中, 將其加熱到半熔化 、 熔化或氣化狀態(tài), 并在沖擊力的作用下將 其沉積到晶體上,從而獲得具有各種功能的靶材( 如圖 1) 。
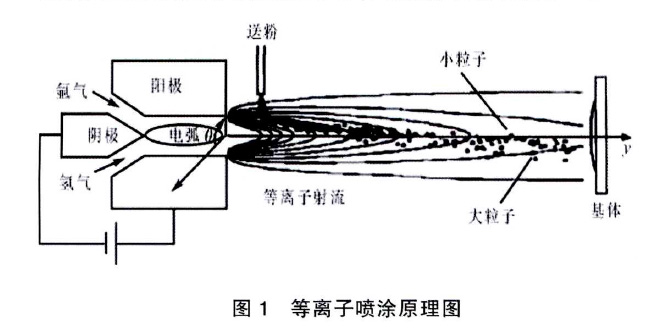
2、等離子噴涂技術(shù)的特點(diǎn)
等離子噴涂具有如下特點(diǎn):(1)等離子噴涂的焰流溫度高, 熱量集中, 幾乎能融化所有高熔點(diǎn)的粉末材料, 可以根據(jù)工件表面性能要求制備出各種性能的涂層;(2)等離子焰流噴射速度高 , 能使粉末獲得較大的動(dòng)能和較高的溫度,涂層與基體結(jié)合強(qiáng)度高;(3)噴涂層平整光滑,厚度精確可控,直接進(jìn)行精加工即可獲得產(chǎn)品,是一種凈尺寸成形制備方法 , 節(jié)省材料 , 特別適合貴重金屈涂層及靶材的制備;(4)等離子噴涂通過采用真空密閉, 通入還原性 氣體、惰性氣體保護(hù)等方法, 可獲得氧含量低、雜質(zhì)少的涂層; (5) 采用高能等離子噴涂設(shè)備 、粉末沉積率高,沉積速度快, 可獲得較厚的涂層, 這是制備濺射靶材的重要保證。
3、等離子噴涂設(shè)備
等離子噴涂設(shè)備主要由等離子噴涂電源、等離子噴槍、 控制柜、送粉器裝置等組成(如圖 2 ) 。等離子噴涂電源是等離子射流能拭提供裝置 , 其工作電流和電壓是影響涂層質(zhì)量的重要參數(shù)。噴槍是集所有噴涂所用的電、氣、粉、水于一體的核心裝置,為噴涂材料的融化、細(xì)化及其噴涂能力轉(zhuǎn)換提供空間, 噴槍設(shè)計(jì)的好壞直接影響到噴涂涂層的質(zhì)量及噴涂效率,這兩者是等離子啖涂系統(tǒng)中最為關(guān)鍵的部件。
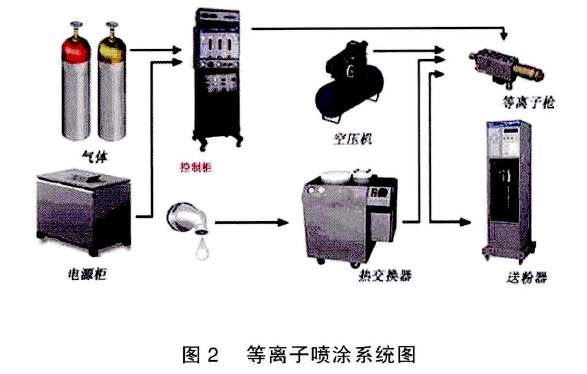
4、影響等離子噴涂制備濺射靶材效果的技術(shù)因素
4.1 電弧功率
電弧功率過高會(huì)使等離子體電離度增加,火焰溫度升高, 可能會(huì)使噴涂材料氣化而引起涂層成分改變。功率過低會(huì)引起粉末顆粒加熱不足,涂層粘接強(qiáng)度低,硬度和沉積效率低。
4.2 供粉系統(tǒng)
供粉速度應(yīng)與輸入功率相適應(yīng)。一般來說,粉末送到焰心才能使其獲得最好的加熱和最高的速度。
4.3 噴涂距離和噴涂角
噴涂材料及其涂層的特征對噴涂距離很敏感。噴涂距離過大,粉末的溫度和速度下降.結(jié)合力、噴涂效率都會(huì)明顯下降; 過小會(huì)使基體表面溫度過高,影響涂層結(jié)合。在基體溫度允許的情況下,噴涂距離適當(dāng)小些為好。噴涂角,一般應(yīng)大于45度.噴涂角過小會(huì)導(dǎo)致“陰影效應(yīng)",涂層中會(huì)出現(xiàn)空穴,造成涂層疏松。
4.4 基體的溫度控制
在噴涂前把工件預(yù)熱到噴涂所需要的溫度.然后對工件采取噴氣等冷卻措施,使其保持恒定溫度。
4.5 噴涂壓力
在金屬材料的噴涂過程中一般采取低壓等離子噴涂(也叫真空等離子噴涂),在壓力為4~40 kPa的可控氣氛腔室內(nèi)噴涂。由于工作氣體離子化后, 是在低壓氣氛中邊膨脹邊噴出 , 噴流射速可達(dá)到超音速, 適合對氧化敏感的金屬材料的噴涂。對于氧化物陶瓷可采用水穩(wěn)等離子噴涂,其能量密度高, 燃燒穩(wěn)定, 噴涂效率高。
5、等離子噴涂制備濺射靶材中存在的問題
等離子噴涂在 濺射靶材 制備方面有著巨大潛力( 如圖 3 ),但同時(shí)該方法也存在一個(gè)重要缺陷, 那就是噴涂組織的多孔性。使其制造的靶材相對密度只能達(dá)到85%~95% , 靶材純度一般在99.5%~99.9%之間。而組織的疏松多孔, 容易吸附雜質(zhì)、濕氣等妨礙濺射過程中高真空的迅速獲得及真空度的穩(wěn)定,并且導(dǎo)致在濺射過程中,靶材濺射表面瞬間高溫使松散顆粒團(tuán)狀掉落,污染被鍍件表面, 影響鍍膜質(zhì)量和鍍膜產(chǎn)品的合格率。另外,若在大氣環(huán)境下 噴涂, 靶材表面 和空氣中的O2和N2, 等氣體大面積接觸, 會(huì)產(chǎn)生大量的氧化物和氮化物雜質(zhì), 即使是真空等離子噴涂技術(shù) ,也不能完全避免合金靶材中氧化物和氮化物的產(chǎn)生。因此, 噴涂靶材在濺射前必須用隔離的前級泵除去表面吸附氣, 從而提高濺射速率和質(zhì)量。
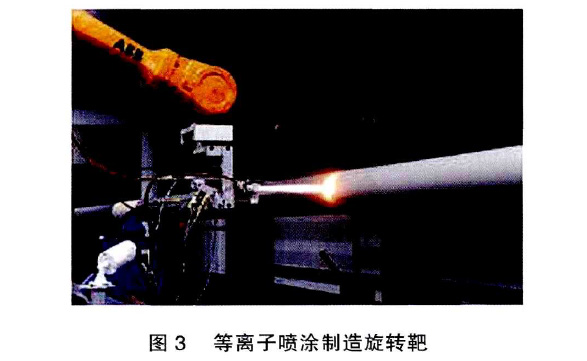
四、等離子噴涂制備濺射靶材發(fā)展趨勢
等離子噴涂法僅需要更換成塑粉末和工藝參數(shù)就能夠制備范圍廣泛的各種材料的大型平面靶和旋轉(zhuǎn)靶。隨著等離子噴涂技術(shù)的發(fā)展, 勢必會(huì)引起濺射靶材制備技術(shù)的重大變革。目前等離子噴涂技術(shù)仍需進(jìn)行以下幾方面的研究 :一是合理選擇噴涂工藝,優(yōu)化工藝參數(shù)、 改善粉末受熱和熔化狀態(tài), 減少環(huán)境對高溫離子的污染和氧化, 形成性能優(yōu)良的濺射靶材。二是進(jìn)一步研究涂層形成機(jī)理、孔隙形成機(jī)理, 尋求消除或減少孔隙率的辦法。三是進(jìn)一步研究涂層與基體的結(jié)合機(jī)理,提高涂層強(qiáng)度。
相關(guān)鏈接